The buildings selected for the corrosion investigations ranged from 5-44 years in age. Surprisingly, the age of the system piping did not directly correlate to the severity of the corrosion found. Rather, the two primary factors influencing the amount of metal loss found was the system design/layout and the amount of activity the system had seen since the initial install. The design/layout of the systems can be grouped into three categories:
- Flat system, with little to no pitch on the branch line or main piping
- Pitched system, with the branch lines running upslope and terminating at the roof/system peak
- Pitched system, with the branch lines running flat, parallel to the slop of the roof
Flat System, Little to no Pitch to System Piping
Those systems that had experienced the least amount of corrosion, including the oldest 44-year-old systems, were installed relatively flat. This configuration results in trapped air being spread throughout the system, rather than localized to any one point. While corrosion still occurs, the metal loss is spread out throughout the system, limiting the severity of resulting oxygen corrosion.
|
Figure 1: 14-Year-Old Flat System - Pocket of Trapped Air in Branch Line with Limited Corrosion
|
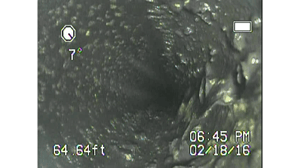 Figure 2: 15-Year-Old Pitched System – Large Pocket of Trapped Air at System High Point |
Pitched System, Branch Lines Running Up Slope
The most significant metal loss was found in those systems whose branch lines followed the slope of the building's roof and terminated at a system high point. This configuration allows all the trapped air in the system to migrate and accumulate at the end of the branch lines, resulting in highly localized corrosion. While this leaves the rest of the system primarily water-filled and in good condition, a leak will develop very quickly at the air/water interface near the system high point where water meets air.
|
Pitched System, Branch Lines Run Flat Parallel to the Slope of the Roof
A third subset of systems are those that follow the pitch of the roof, but the branch lines run flat parallel to this pitch. When the lines are fed by riser nipples off the top of the main, every branch line will act to trap air. However, those branch lines closer to the peak of the system will contain a larger pocket of trapped air.
The last factor that heavily influences to the severity of corrosion in wet system piping is the frequency with which it is drained and filled. The primary ingress of fresh air into the system piping occurs during drain downs. Those systems that had been relatively untouched since initial install appeared to be in excellent condition, while those that had undergone large scale tenant modification projects that required frequent draining and filling had experienced significant metal loss.
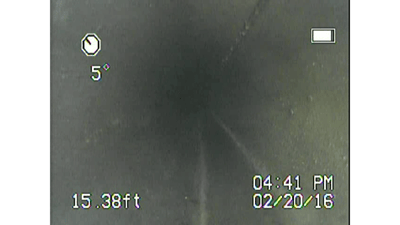 Figure 3: 28-Year-Old System - Low Branch Line, Small Pocket of Trapped Air |
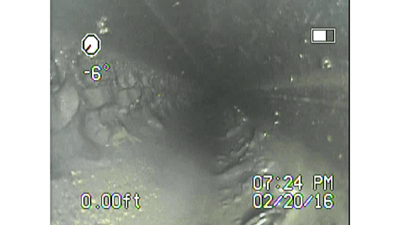 Figure 4: 28-Year-Old System - High Point Branch Line, Large Pocket of Trapped Air |